Yorkshire Rose, hull #133, was built by Catalina Yachts during their first
full production year. At that time, CY didn't even plan for a anchor
windlass. For all the years I've owned Rose, I've raised the anchor by
hand and muscle. And wished for a windlass most of those times.
I've eyeballed the Lewmar Anchorman, a low profile manual windlass for a
while, but kept putting it off. Finally, the time came (i.e. I got
married) to stop procrastinating.
During a boat show, I talked to the Lewmar representative and learned that
they had an electric version of the Anchorman. They had discontinued
this line but the local vendor still had one on his shelf. So out flew
the credit card....
Now came the challenge: where to mount this thing. Fortunately, a
couple years ago, Mike Smith did a
similar installation. So, following in Mike's footsteps, I tackled
this project. What follows is the nitty gritty details.
1. The windlass motor requires protection from the elements. Since
there's no "box" in the anchor well on the early model C34 boats, my best
option was to put the motor inside the V berth. That, of course, meant
cutting and drilling into the deck above the V berth. And then
creating a water tight seal between the flat surfaces of the windlass
capstan and windlass motor and the curved surfaces of the deck and the cabin
ceiling. YIKES!!!!
I started out with the idea that I'd get some 1/4" teak plank, cut it to the
correct outline of the windlass parts, then meticulously sand one side of
each to match the curvature of the deck or ceiling. Fortunately, about
the time I was ready to start the sanding part of that job, I read in the
Mainsheet about another owner who needed a flat level surface for mounting
his new, extra starter battery. He described how he created this by
pouring unthickened West Systems epoxy into a mold right on his hull's
fiberglass. And the proverbial "light came on" in my head. This
would work great for the top side, which is the part that truly needed the
watertight seal.
After that, it was all just details. The pictures below show the
details as the project progressed.
Day 1 at the boat. First I sanded down the deck where the
capstan will be mounted to remove the gel coat and to rough up the surface.
After drilling a pilot hole to mark the center, where the shaft hole will
eventually be cut, the mold was taped down and then lined with modelling
clay. The clay prevents the epoxy from permanently attaching the mold
to the deck! The mold was made from a piece of Masonite. Easily
started with a jigsaw and finished Xacto knife.
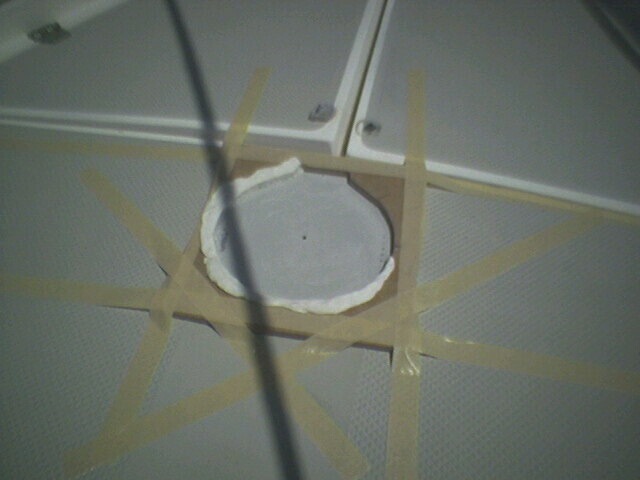
Mixed up the epoxy and poured it into the mold. A prior practice
session at home taught me that no matter how carefully I mixed the epoxy and
hardener, air bubbles would get trapped into the fluid. But the
solution was simple, pop the bubbles (with the toothpick) before the fluid
started to harden.
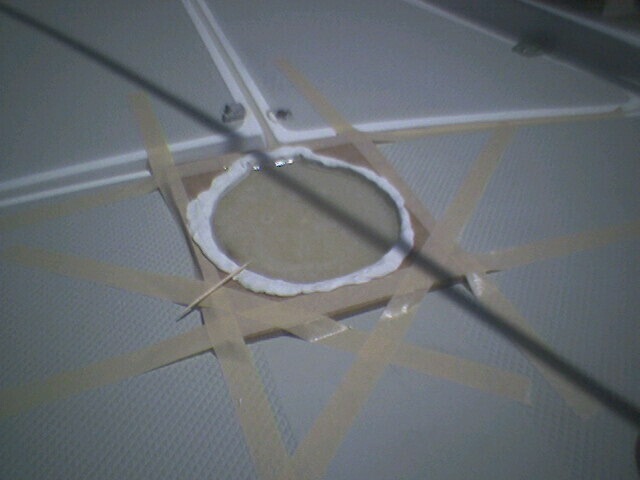
After a couple hours, the epoxy hardened enough that the mold could be
removed. I mixed another small batch of thickened epoxy and applied
that around the edge to create the fillet before the pad cured too much.
I did all this on a Sunday and let it finish curing during the week.
The epoxy doesn't need that long to cure, but the next steps would require
two days to do right and I wanted those to be consecutive to minimize my
exposed "hole" time.
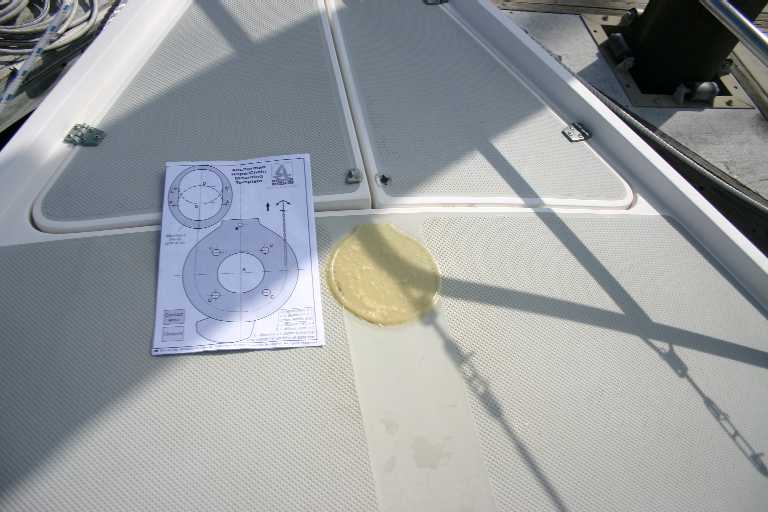
Day 2 at the boat. Now came that really scary part.
Holes, including a really big one, in the deck. I didn't know how
thick the deck is at this location, nor how much is fiberglass shell and how
much is wood core. It turned out to be 7/8 inch thick. From top
to bottom: 1/8 inch fiberglass, 3/8 inch plywood, 3/8 inch fiberglass.
My epoxy pad added another 1/8 to the top.
After drilling the holes, I had to gouge out the plywood exposed at the edge
of each hole. Additional epoxy will replace the removed wood to both
seal and strengthen the holes against the compression forces of the mounting
bolts. Here's my gouging tool.
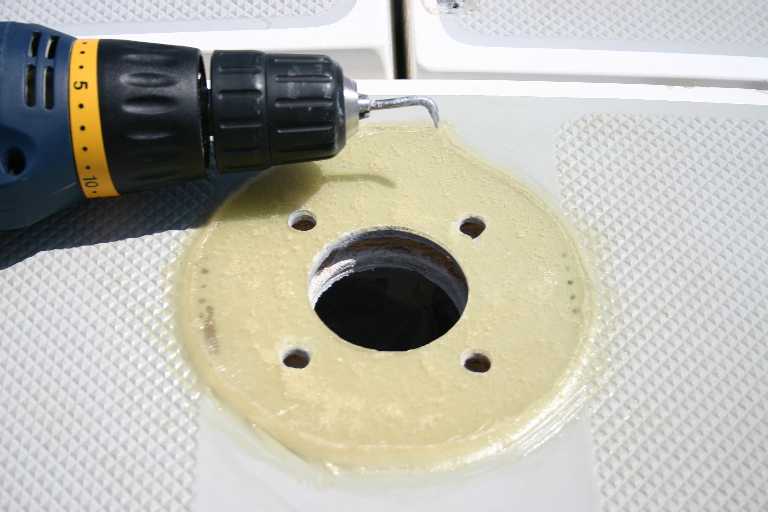
Of course, all the drilling and gouging creates a mighty mess. But a
plastic garbage bag and some masking tape helped to contain a large part of
it.
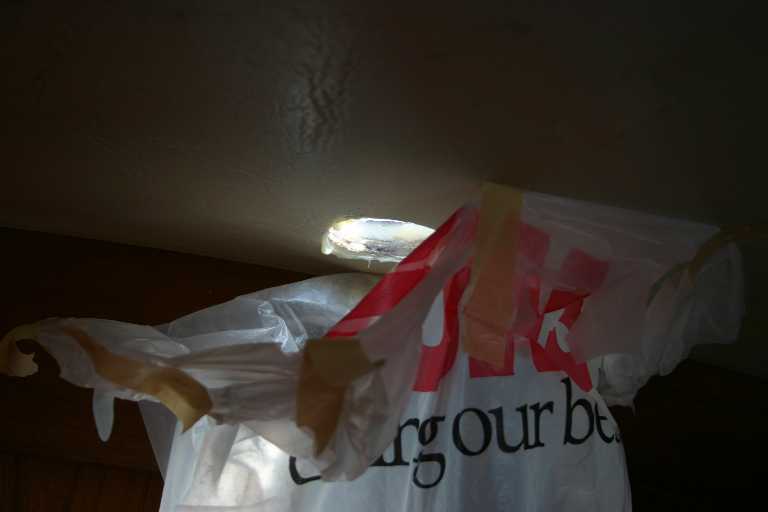
The materials and tools needed to fill and seal the holes. First I
mixed a batch of thickened epoxy and sealed the big center hole. That
was smeared into the gap where the plywood had been removed. I had to
do the center hole first first because the plywood between the center and
side holes had broken through in a couple places. After the center was
sealed, then I mixed an unthickened batch and used a syringe to inject the
fluid into the bolt holes.
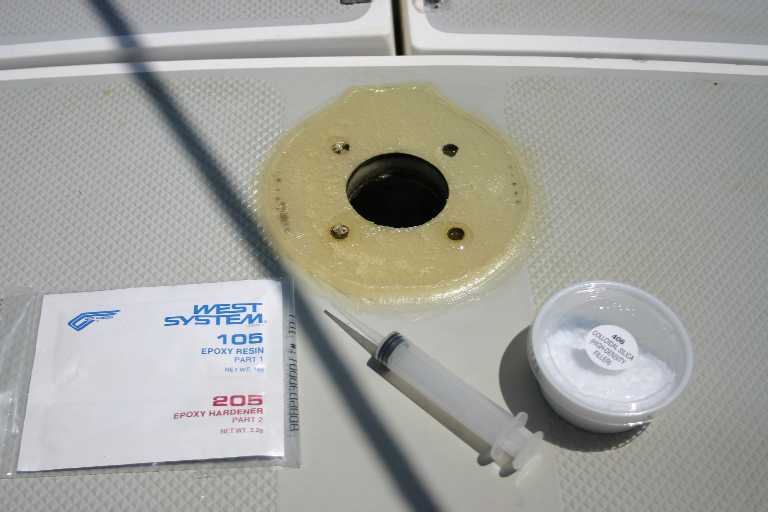
Day 3 at the boat. With the epoxy hardened, I simply had to
redrill the mounting holes and then sand down the top surface to get that
final smooth flat surface.
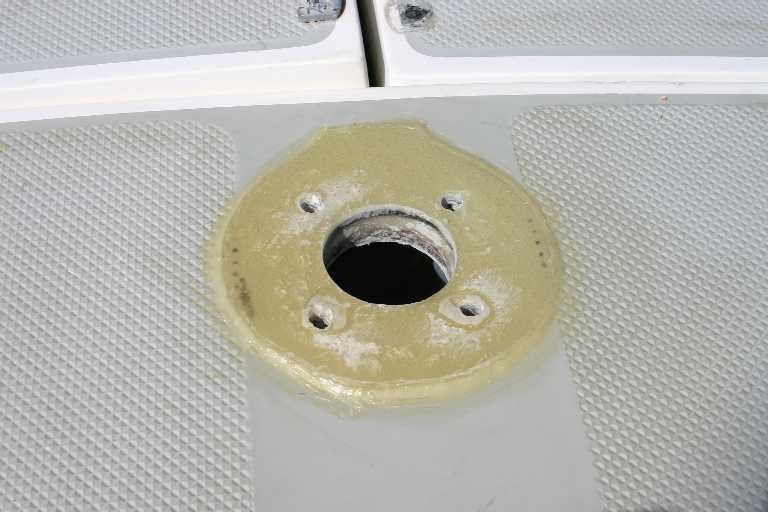
Sanding epoxy can be quite messy. And normal shop vacuums are not
quite as handy around a boat as they seem to be in the garage. But a
little ingenuity (and luck) is all it takes. My car vacuum's accessory
attachment piece just happened to fit snugly into the sander's exhaust port
and did a better job of pulling the dust away than the sander's catch bag
would have done.
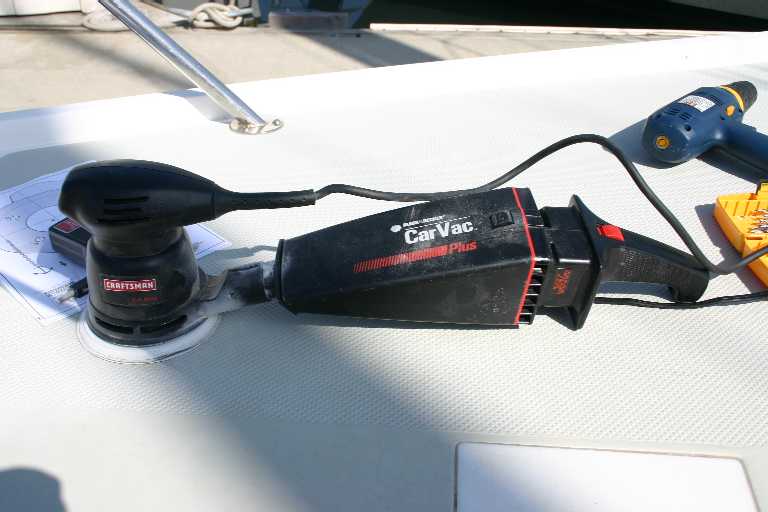
Now just test fit the capstan. Perfecto!
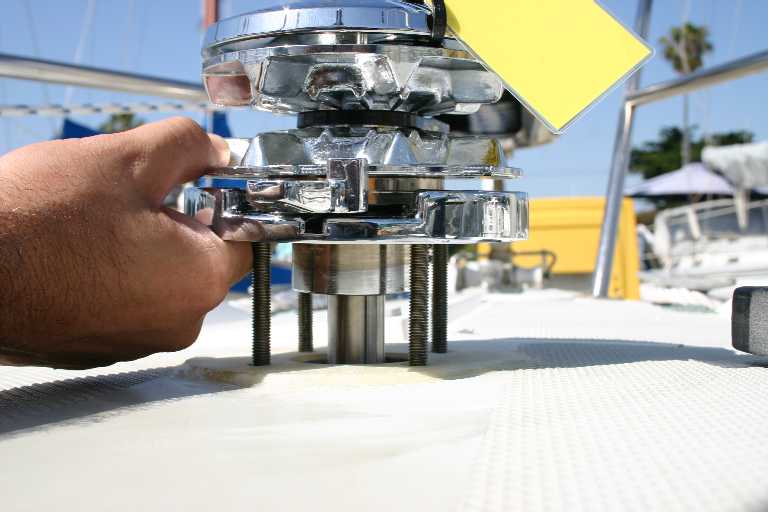
A coating of topside hull paint makes it look almost professional, and adds
a layer of weather and UV protection to the epoxy pad.
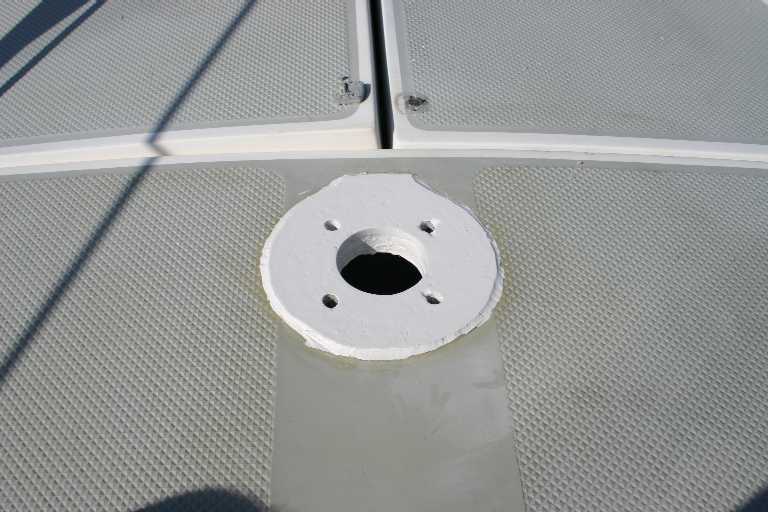
Finally, apply a bead of 3M's 4200 around the holes and the outer ring of
the pad. Slip the capstan into place.
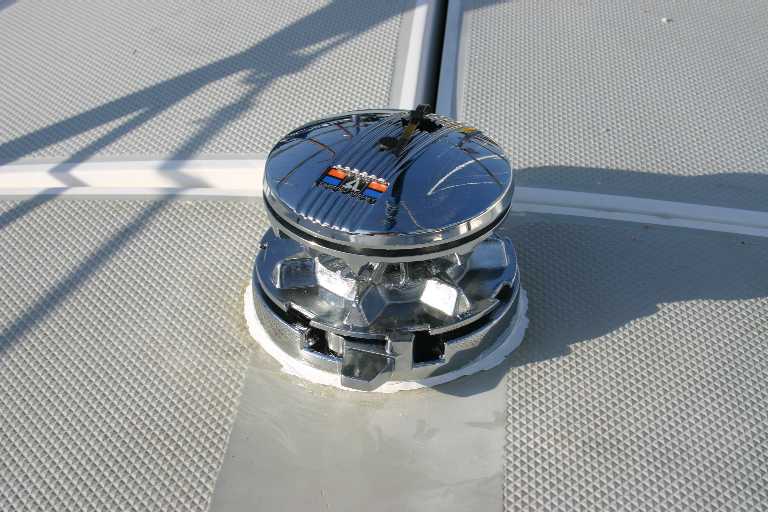
Inside the cabin, I kept my original idea of a shaped teak pad. It's
kind of hard to duplicate what I did topside when gravity is fighting you
all the way. Anyway, I just lightly finger tightened the nuts to the
bolts while the 4200 cured and called it a day.
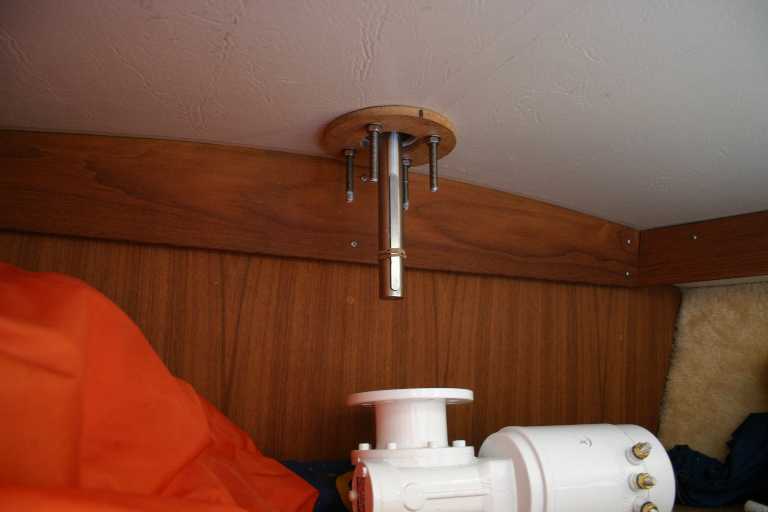
Day 4 at the boat. Time to mount the motor. But first try
showed a major problem. The threaded-rod bolts are too long. The
bottom out against the motor body itself before the top mounting surface got
to the ceiling. Only two choices now: get shorter bolts or a much
thicker wood pad. I chose the former. So with the capstan still
in place, I removed and replaced each bolt with one that was correctly
sized.
Day 4 and 5 at the boat. Now that the motor and power switching
solenoid were in place, it was time to connect the 12V power. First I
removed the forward trim panel to see where I could route the wire and
controls. Turned out fortunately. There's a little gap between
the anchor well side and the hull on the starboard side that has access to
the bilge under the anchor well. This gap was actually created by a
molded "hanger" for Danforth style anchor flukes. (Shown several
pictures below) So I fished a lead line down and then pulled the power
cables back up. After agonizing momentarily, I bit the bullet and
drilled the slotted hole in the forward trim panel and fed the cables
through.
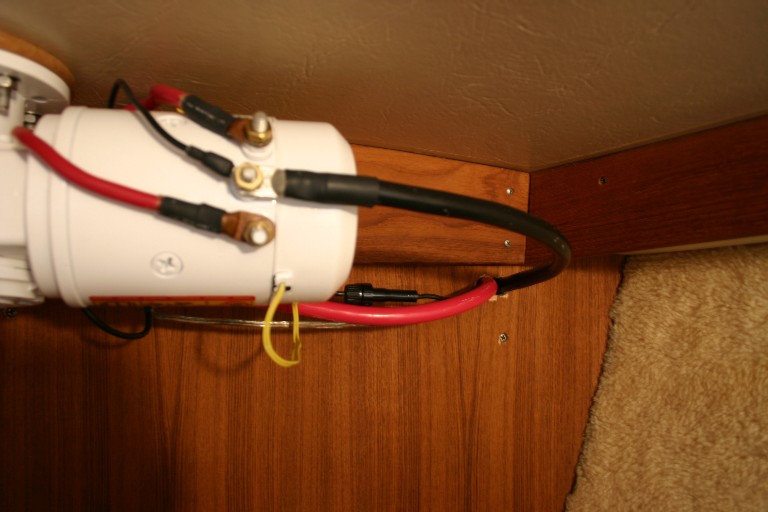
The control solenoid is mounted to the forward cabin wall, behind the motor
body.
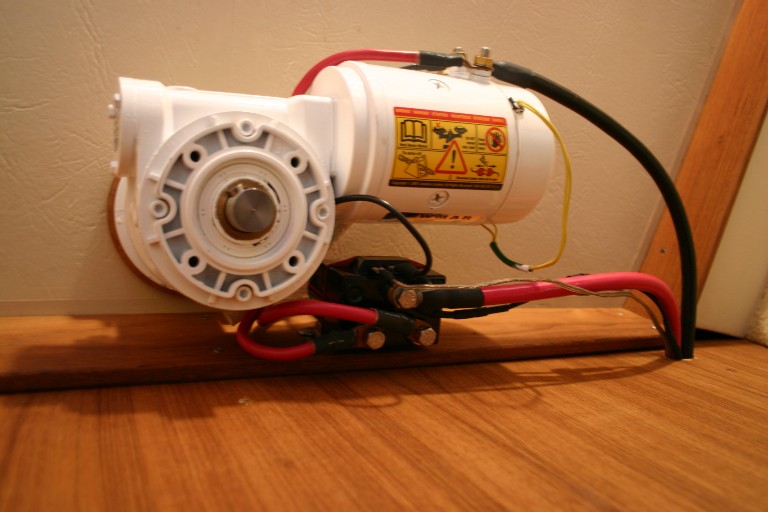
I made the hand controller from a marine weatherized rocker switch, a
plastic "hobby box" from Radio Shack, three strands of marine 16 AWG wire,
and a marine weatherized deck connector. The deck fitting piece neatly
fit onto the Danforth hanger in the anchor well, and is only inches forward
of the V-berth forward bulkhead wall.
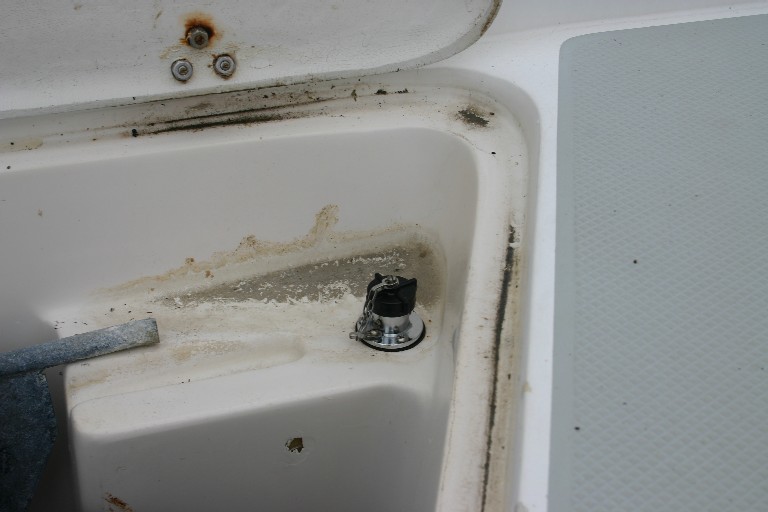
Day 6 at the boat. The power cables are routed back to the
battery box along the starboard hull. Under the V-berth I secured the
cables with screw anchorable cable ties to the underside of the V-berth
sole. The cables then pass through the hanging locker walls into the
main cabin, under the starboard settee. Still following the starboard
hull until they finally turn toward the battery box, crossing on top of the
water tank. Inside the battery box, the ground is secured to the
negative side busbar. The 12V cable leads to the circuit breaker,
newly mounted in the battery box wall.
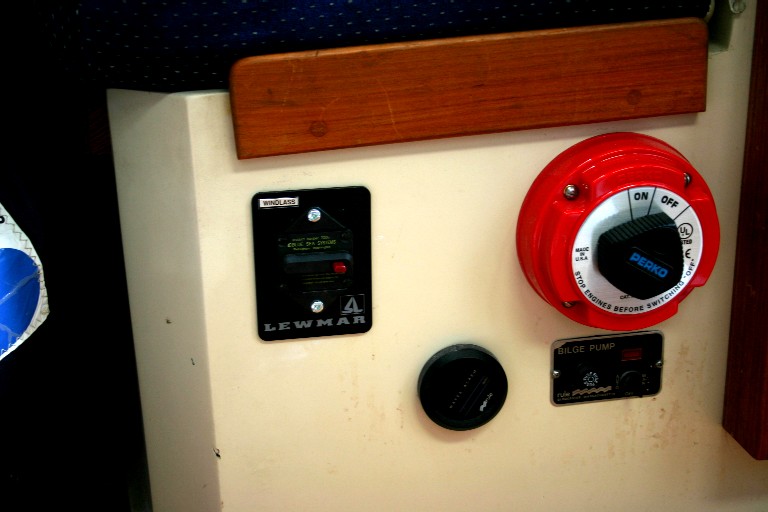
Day 7 at the boat. After the test run, the exposed power studs
and covered by rubber caps and the wires are neatly dressed with cable ties.
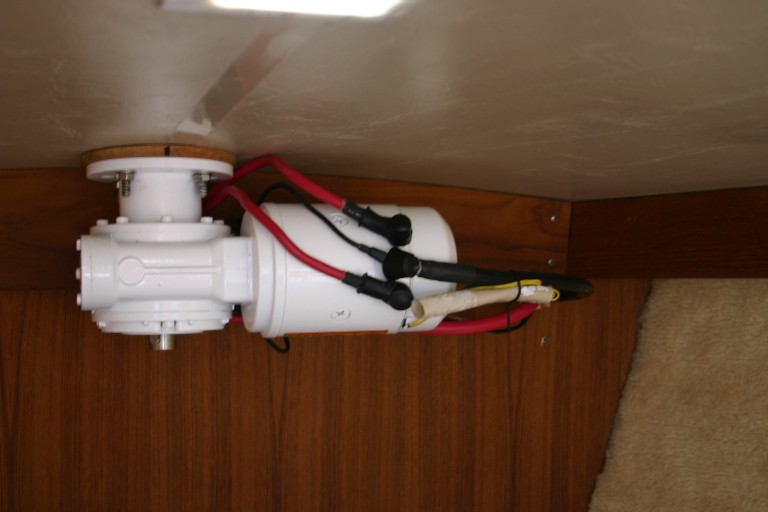
I've only tested the anchor windlass in the harbor. But we're now
ready for the next cruise.
Oh, one more thing. My mate thinks the motor is an eyesore. So
that's prompted the next
project. Mark Elkin
Yorkshire Rose #133 |