Windlass Inside Double Door Anchor Well
For over 19 years I’ve always wanted a windlass. However, the first
production year of the C34 that had an anchor well specifically made for a
windlass was 1989 – the year after APACHE was built! That molded in box in
the right rear corner of the anchor well was made to hold a horizontal
windlass. Catalina also went to a single anchor well door for that and
subsequent C34 production years. I have never liked the windlass on the deck
(and aft of the anchor well) with the motor extending down into the V-berth,
as some C34 1986/87/88 owners had done. I wanted a clean deck. A search of
the C30, C34 and C36 owner data found that no one had installed a windlass
inside a double door anchor well, which is where I wanted mine mounted! I
had always been meaning to come up with a design for that installation. I
suddenly found that I was the owner of bilateral inguinal hernias and
pulling the anchor/chain was no longer an option. My need for a suitable
design rapidly moved to the top of my “to do” list!!
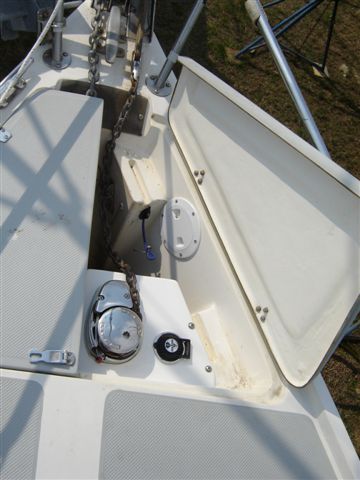
Windlass one door closed
The major unknowns were to first select a windlass and then figure out
how to secure it inside the anchor well. The factory uses a horizontal
windlass with the motor at 90 degrees. With an “open” anchor well I decided
to use a vertical windlass. A vertical windlass has some nice advantages
over a horizontal one. It was lighter in weight and can use a smaller motor
because there is no 90 degree turning mechanism. A few other nice features
were that the chain/rode was in the gypsy about 160 degrees rather than 90
degrees for a horizontal version. This alleviates the problem of the chain
not fully engaging the “teeth” of the gypsy. Verticals also seemed to be a
lower price, I’ll guess because they didn’t have that 90 degree turning
mechanism. The main vertical disadvantage was that I couldn’t have both a
drum and a gypsy because it would be mounted too low in the anchor well. I
decided on a vertical with a gypsy that could handle both line and chain. I
selected the new Lewmar V700 and a search of the internet found much better
pricing than in any of the Marine chandleries! That internet pricing was
also much cheaper for the marine grade wire, connectors, heat shrink and
split loom wire covering.
After selecting the Lewmar V700 the big problem was what was behind that
teak bulkhead at the head of the V-berth so I could figure out: 1. How to
route the primary power wiring? 2. Where to mount/install the solenoid
(control box)? 3. How to run the motor and the foot switch wires to the
solenoid? 4. The least of my problems was where to install the circuit
breaker and where to connect into the battery/s.
I had installed a second shelf above the factory shelf at the foot of the
V-berth, so they both had to be removed. I decided to route the power wire
along the starboard side of the boat, because I had a starting battery just
forward of the starboard water tank. I then removed the underside Naugahyde
covered plywood strip that runs the length of the starboard V-berth just
under the cabin light. This strip hides the wiring from the bow for the
starboard side cabin lights. Next to come off was the center teak facing
strip on the top of the teak bulkhead above where the shelves used to be.
Then I had to take off the cabin light by removing the screws and cutting
the wires. Next was to remove the screws on the vertical starboard V-berth
teak facing piece. This long strip of teak was a little difficult to get out
because it was tightly fit into place. Now I could see from the upper
corner, that the teak bulkhead was a piece of ½ inch teak veneer plywood
that was perfectly cut to fit and touch all sides of the hull liner and the
V-berth platform. I drilled out the 6 teak plugs and removed the screws that
held the teak bulkhead in place. The teak bulkhead pulled right off.
However, to my surprise I found that a piece of ¾ inch plywood with about a
1 inch gap on all sides had been caulked/glued to the cabin side of the
anchor well! I still didn’t have a clear view/idea of what the cabin side of
the anchor well really looked like. I suspected that the aft molded portion
that was made to hold the Danforth type anchor was hollow, but I still
couldn’t see that. After a few mighty pulls on that plywood it finally broke
loose leaving some of one “ply” still glued to the cabin side of the anchor
well. Finally I could see the entire cabin side of the anchor well and those
Danforth indentations were in fact hollow on the inside.
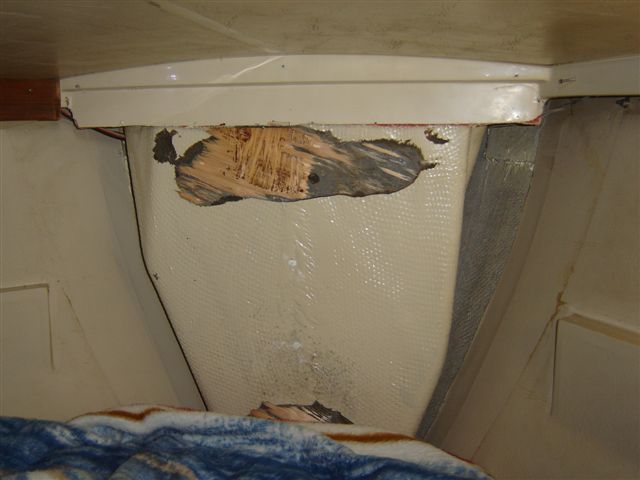
Windlass V-berth anchor well side
Now that I knew what the anchor well looked like from the inside I
determined that the two pieces of plywood together (1 ¼ inches thick) would
make an adequate “backing plate”. In between tearing up the V-berth I was
designing a bracket to hold the windlass and where it would be
placed/mounted inside the anchor well. I measured the height of the V700
from its mounting base to the top. That measurement was 2-5/8 inches. I made
a flat cardboard cut out of that design and found that the top of the aft
starboard Danforth mold could support one side of the windlass bracket,
would also be horizontally deep enough to close the anchor well starboard
door all the way and the windlass would align with the chain run from the
bow roller. (I installed my bow anchor roller. The 1989 was the 1st
production year for a factory installed bow roller). From that flat piece of
cardboard I made a three dimensional cardboard/duct tape model adding a back
and a gusset port side for extra support.
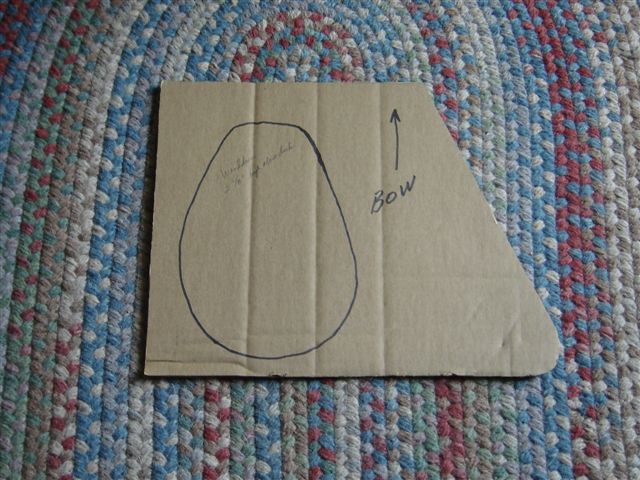
Windlass top cut out
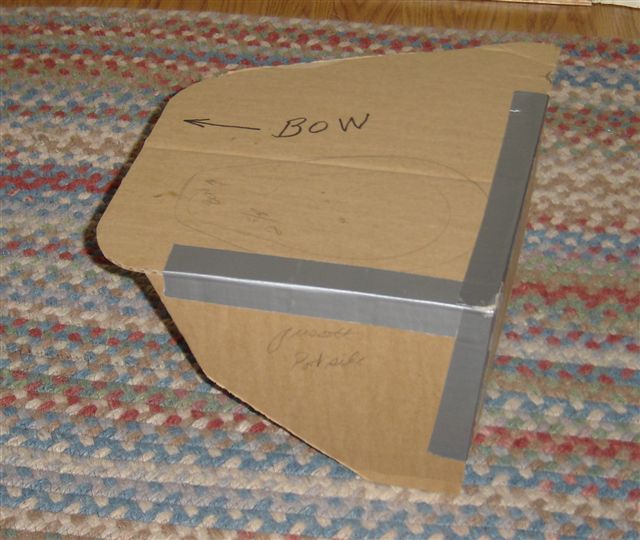
Windlass cut out 3D
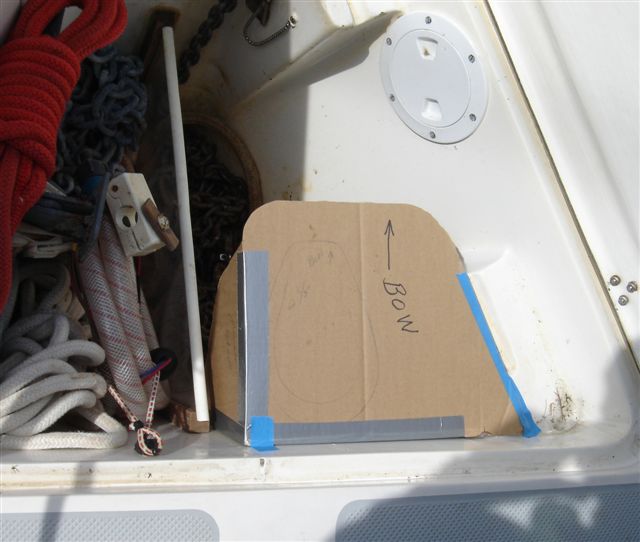
Windlass cutout installed
The next step was to mix up some West System (epoxy) and lay up
alternating layers of mat and cloth over the waxed paper covered model,
soaking down each layer with the epoxy until a 3/8 inch thickness was
attained (10 layers). After the epoxy set overnight it was trimmed, sanded
and sprayed with a gelcoat primer. I also rechecked to make sure that it was
an exact replica of my cardboard model. Then I made the cutout hole so the
windlass would fit in the bracket and drilled 4 mounting bracket holes in
the back, making sure that the windlass motor would not block those holes! I
was satisfied that my homemade bracket was strong enough to handle the
torque of the windlass. The bracket is surprisingly heavy!

Windlass platform cardboard to fiberglass
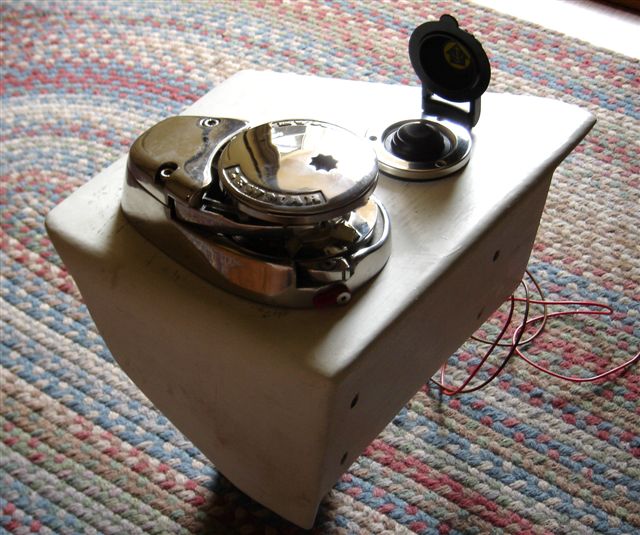
Windlass & footswitch in platform
Lewmar recommended #4 gauge wire for runs much longer than the 18 feet
that I estimated I would need from the starting battery (just forward of the
starboard water tank) to the anchor well. I initially thought that the wire
would run from the starting battery, under the settee, and go up thru the
front of the salon sliding compartment, into the cabin light wire run under
the starboard salon deck. I found there was no space under the slider as the
hull liner and hull became one! The only other route was thru the bottom of
the hanging locker, up the hull inside the locker and come out thru the
counter top in the far aft outboard corner of the top of the hanging locker.
That worked and the wire then went up to join with and parallel the cabin
light wire toward the anchor locker (the run was16 feet long) I use that
corner to stack all of my engine and other equipment manuals, so they would
cover the wire. After that wire route was decided upon, the placement of the
circuit breaker under the forward starboard settee was obvious. The breaker
was easy to install between the battery and the + wire going into the
hanging locker.
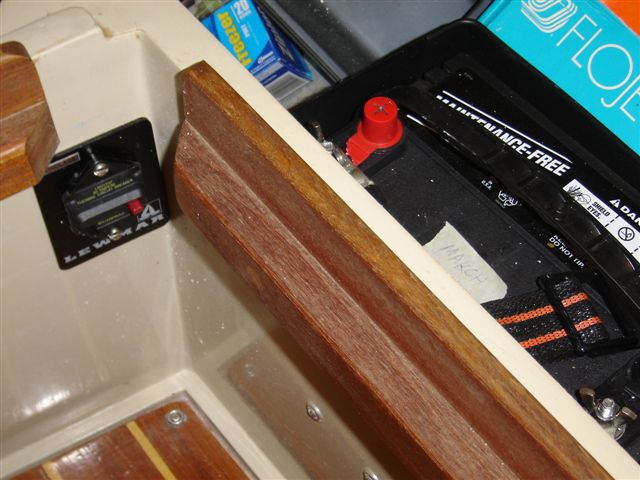
Windlass circuit breaker
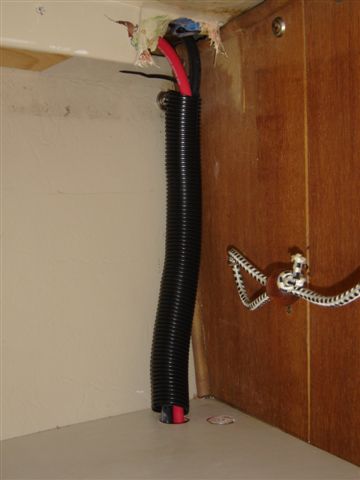
Windlass wires exiting hanging locker
Next was where to install the solenoid. It was a tough choice, but I
decided to mount it on the starboard hull high just inside where the plywood
bulkheads would be reinstalled. I had dabbled with the idea of running the
wires from the foot switch and the windlass motor thru the bulkheads and
then mounting the solenoid on the V-berth side of those bulkheads. I didn’t
want to drill extra holes thru the teak bulkhead, so time will tell if I
made a wise decision. [There is also another wire routing option of
connecting into the battery selector switch for power, and running the wires
inside the vertical port side teak that covers the holding tank vent. The
breaker could be mounted in the panel or in that teak face cover and join
the windlass wires with the running & cabin light wires all the way to the
front of the V-berth. This routing can also be done for 1989 and later
boats, that did not come with a windlass installed. I know of a 1989 and
1990 boat that have done this and mounted the Maxwell 800 in preference to
the smaller 500.]
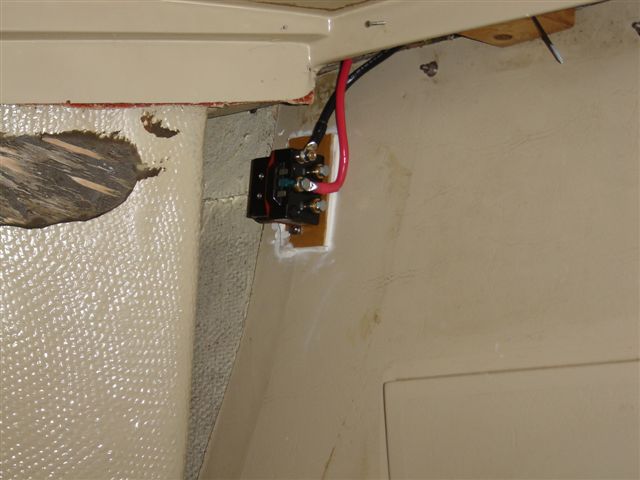
Windlass solenoid starboard side
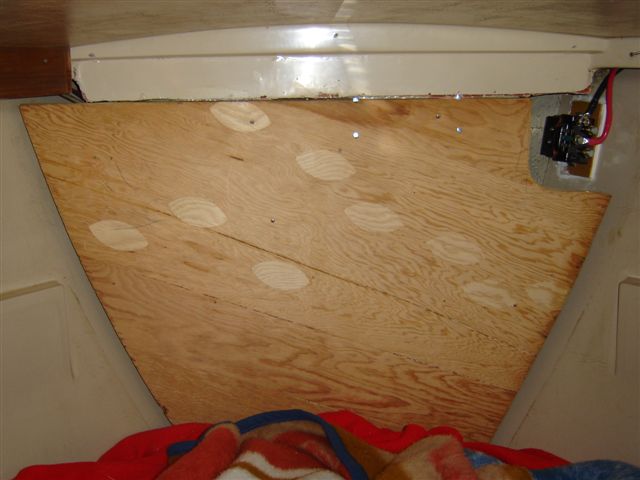
Windlass first plywood bulkhead
The solenoid was mounted on a 3/8 inch thick piece of plywood and caulked
to the hull. I then remounted the ¾ inch plywood bulkhead using caulk and a
few screws to hold it in place. Just previous to that mounting I had cut out
a small upper starboard corner out of the plywood bulkhead. This would
enable me to get at the solenoid and wire when the bulkhead was back in
place. With that ¾ inch bulkhead back in place I could drill the mounting
holes and mount the bracket with windlass and foot switch. Before the final
mounting and securing of the four longitudinal 5/16 inch bolts (thru the
anchor well & plywood bulkhead) and the two ¼ inch bolts (thru the Danforth
mount), the entire mating surfaces (of the back of the bracket and anchor
well wall) were coated with 3M 5200 fast cure sealant. I had also cut some
small ½ inch plywood squares to simulate the ½ inch teak bulkhead so I could
tighten the bolts in place while the sealant cured and also cut the bolts to
the correct length.
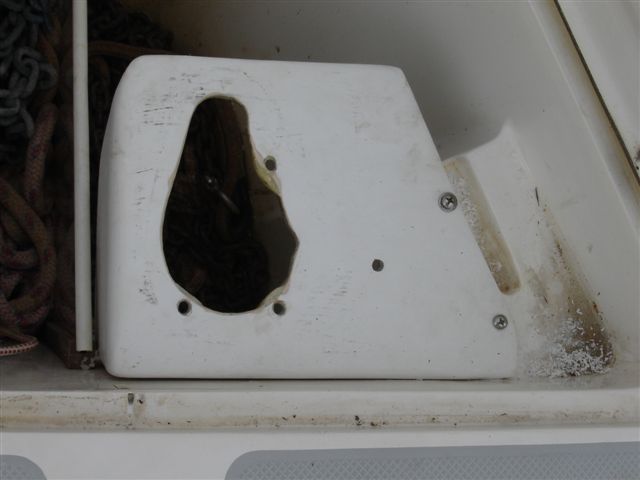
Windlass platform installed
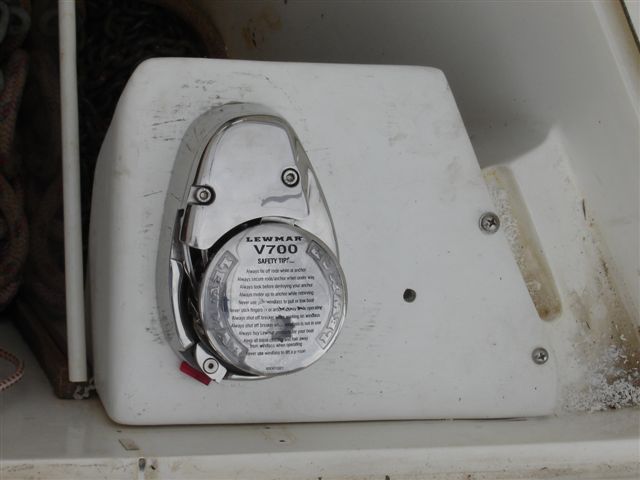
Windlass platform with windlass
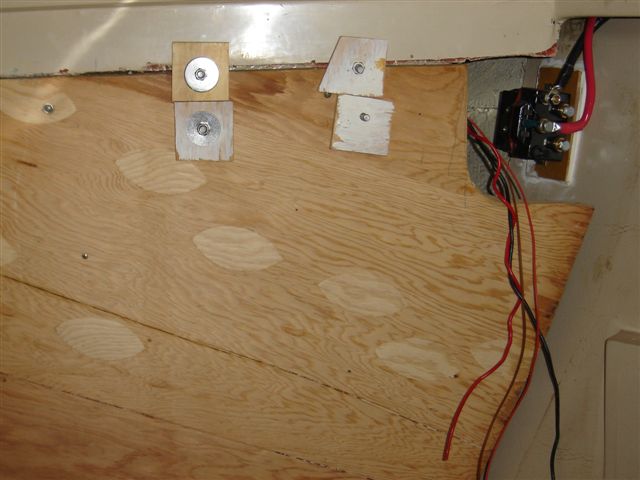
Windlass installed with wiring ready
To connect the wires I cut a ½ inch hole thru the starboard aft side of
the anchor well and inserted a 2 inch piece of ½ inch hose. This hose was
caulked in place and acted as a conduit for the motor and foot switch wires
to go thru. The down angle of the hose was inside the anchor well to inhibit
water from flowing inside. I did not cut/shorten any of those 4 wires, but
got the correct length by making a wire bundle inside the anchor well and
securing that bundle with wire ties. The wires were then connected to the
solenoid and that conduit was filled with caulk on the inside and outside
for waterproofing. After the sealant cured it was time for a test run. To my
surprise I’d reversed the foot switch wires so I had a down rather than an
up switch! That was corrected by simply moving the spade connectors on the
solenoid!
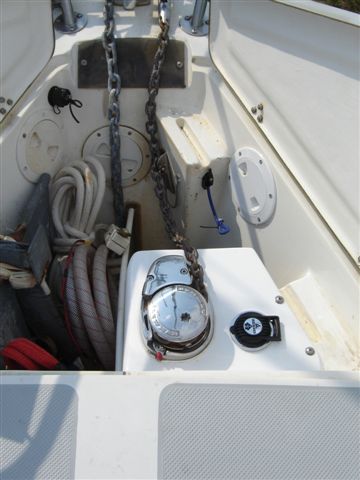
Windlass finished with both doors open
I crimped & soldered all connections and covered each connection with
heat shrink. All paired wires were put in split loom wire covering and all
ring & spade connections were sprayed with BO Shield for protection.
Now it was just a matter of putting everything back together. With the
sealant cured, I pulled the 4 mounting bolts, reinstalled the teak bulk
head, drilled holes thru that teak bulkhead and secured the 4 mounting bolts
with self locking nuts on stainless fender washers. The old mounting holes
in the teak bulkhead were filled with plugs and it was remounted using
screws and finishing washers! Next was replacing the long teak strip on the
starboard side and remounting of the cabin light. The center teak facing
strip went back in place along with the starboard Naugahyde strip underneath
the teak trim. I reinstalled the two V-berth shelves. I dabbed some flat
brown (primer) paint on the stainless washers and nuts so they would blend
in with the color of the teak bulkhead.
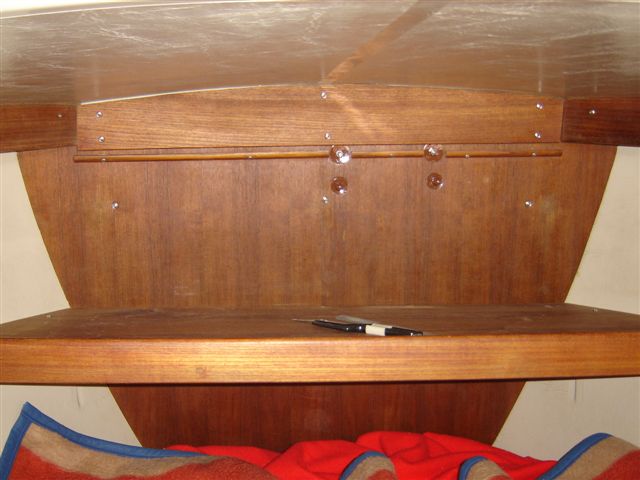
First Shelf
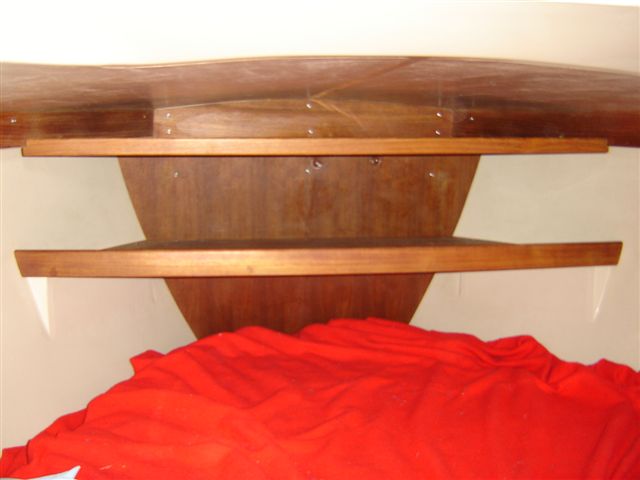
Second Shelf
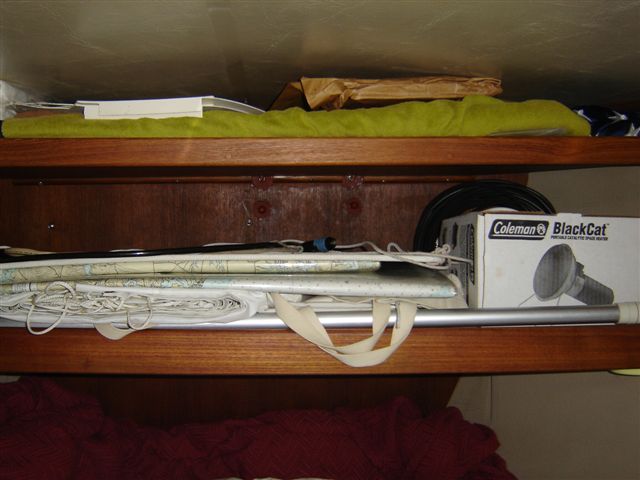
Inside finished
As you could see from the pictures, I was staying on the boat while I was
doing this installation, so the mattress was still on the V-berth (no place
to put it!). The aft cabin was loaded with its normal stuff (cockpit
cushions/throwable cushions/spinnaker/clothing from the forward hanging
locker/etc/etc), so sleeping back there could only have been an option if
everything were moved home! The cockpit was loaded with the dinette table,
starboard salon cushions, seat boards along with the stripping I was
removing and the 2 bulkheads. It’s lucky that I have a full winter cover as
I underestimated how much of the boat I would have to take apart (all at
once!) to do this installation! It sure was tough on your back having to
scrunch down to work in the forward part of the V-berth!!
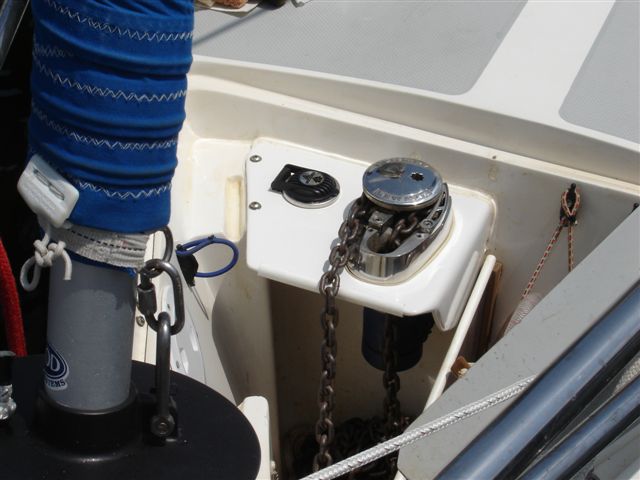
Windlass from bow
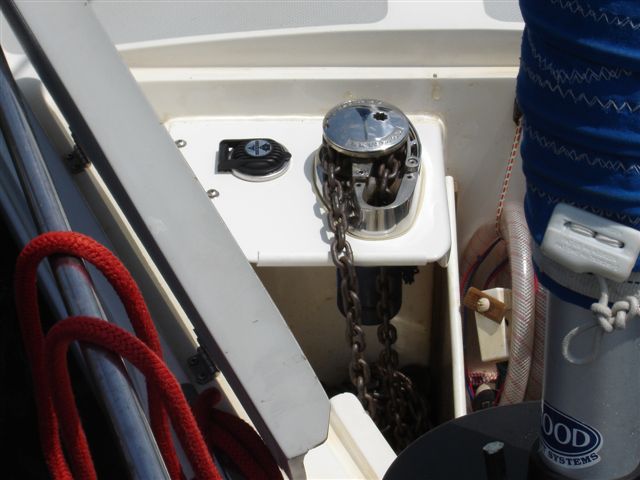
Windlass from bow
The Lewmar V700 I purchased had an installation kit (which included an
up/down Toggle Switch and a Breaker/isolator). I had to replace the toggle
switch as it was not made (or could not withstand) the corrosive wet
environment of an anchor well. That meant I had to purchase an “UP” foot
switch and a solenoid/control box. Even with those additional costs my
installation was still under $900. I was also very lucky because when I made
the bracket, the marina that I was at was doing an insurance job on a 1984
Catalina 30. A gelcoat side of the C30 had been chewed up in a storm. So
when they “shot” that C30 with gelcoat, I had them spray my bracket. The
match was perfect!!
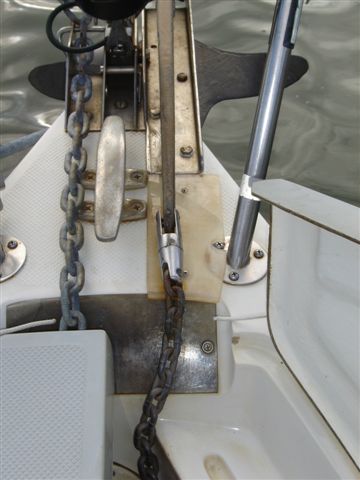
Lexan Chain Guard
After the complete installation was checked for proper operation; I
decided to add a thin narrow piece of Lexan between the end of the bow
roller and the start of the anchor well. This Lexan acts as a buffer (guard)
so the moving chain cannot nick or chip that deck gelcoat.
Ron Hill
APACHE #788
|